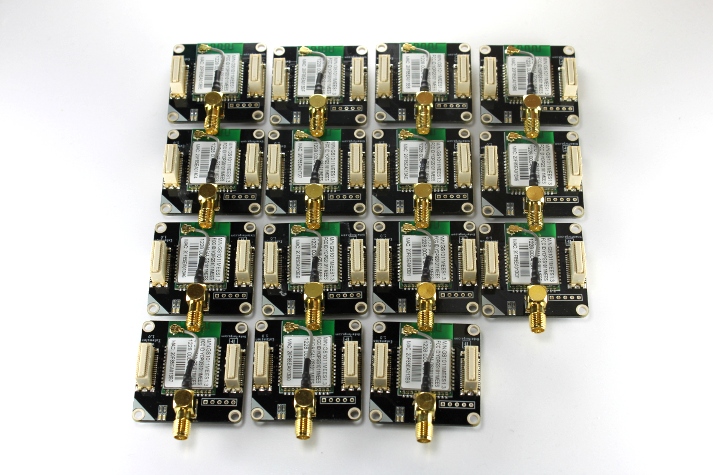
Last Friday our EMS manufacturer produced the first WIFI Extensions. The production preparation was not easy since the WIFI modules are only solderable with a peak temperature of 240°C. We have to produce them lead-free, so this is not an easy task for our manufacturer. Unfortunately the reflow process produced a huge amount of solder bridges.
After some investigation we found the reason for it. Since we were soldering with low temperatures there is not much tolerance for the used materials. It turns out that the surface finish and pad dimensions of the circuit boards do not have the same quality as the circuit boards we got before. The boards are electrically fully usable, but these minor divergences are enough to make troubles. Below is a microscopic image of the stack connector pads of a WIFI Extension (top) and another Extension (bottom):
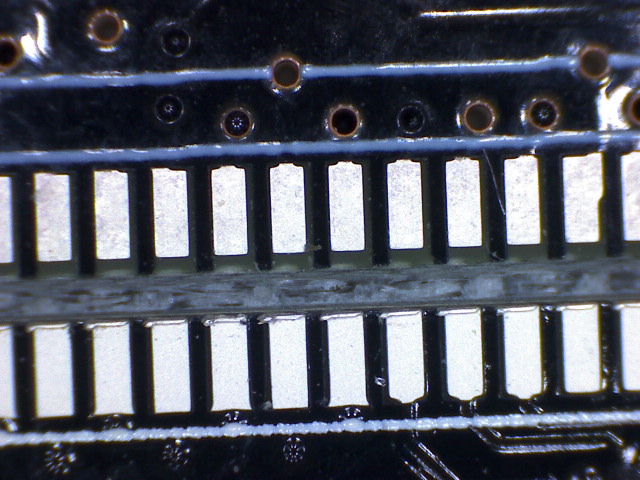
You can see that the pads are for some reason not completely filled in and the surface finish is of poor quality. To solve the soldering problems we ordered modified stencils and another type of soldering paste. We are currently waiting for both to arrive. We will restart production presumably on friday and use the additional time for testing and to implement more WIFI features (more configuration possibilities). If everything works as expected we will add the WIFI Extension to the shop on next Monday.